The generation of large amounts of waste is an accompanying problem of a modern, consumer-oriented society. Waste is an unwanted product of a design process, which has no use value. However, what is a waste for one industry, is a source of raw materials for another. Since zero-waste industries and technologies do not exist, except, conditionally speaking, the food industry that tends towards it, it is necessary to find a solution that will create the conditions for waste minimization through the reuse or recycling and more efficient management of waste.
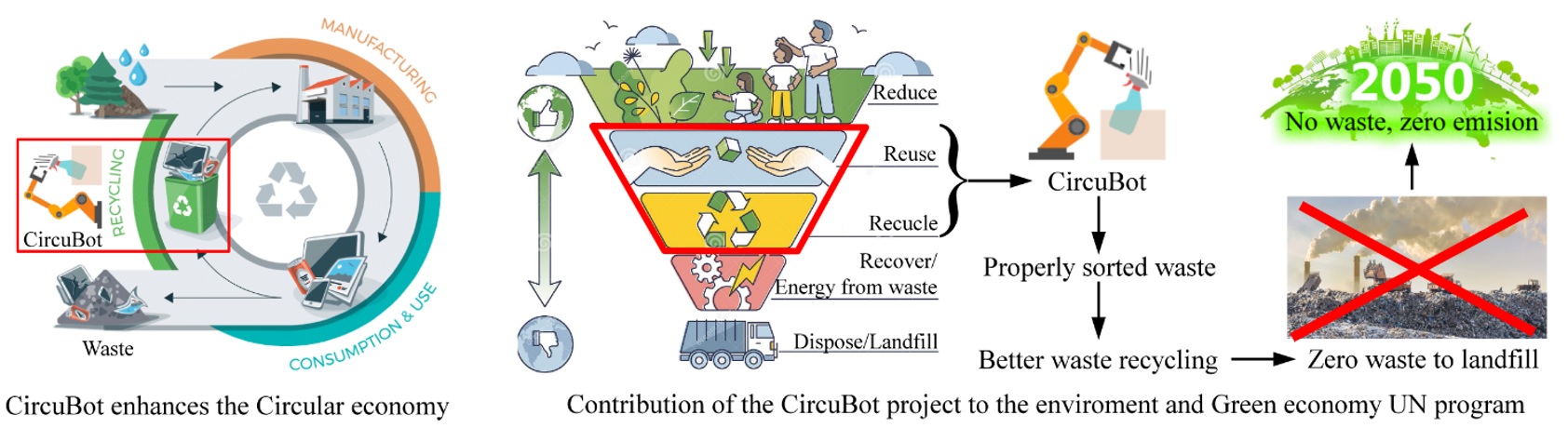
Figure 1. Impact of the CircuBot outcomes on the Circular economy and the UN Green economy 2050 goal.
Improved efficiency and digitization of waste sorting management – Waste sorting plants in Serbia are relying on human factors so the occurrence of flaws in waste sorting and treating commonly results in expensive claims – while the source of flaws commonly remains not possible to find and prevent in the future. Due to the lack of digitalization, there is a high pressure on top-management to be constantly present in the waste sorting halls – whose time could be better invested to enable a company’s business growth.
Improved efficiency of waste handling – Waste management plants in Serbia and beyond adopt different mechanical procedures to sort the waste, such as magnets, rotary sieves, and air separators. While each method is effective per se, it still cannot deal with the significant variability of processed waste. A human worker is still needed at different stages of the recycling process, such as preselection and final sorting and inspection. Thus, humans work in a dusty, dirty environment being in touch with hazardous materials.
Improved waste detection and sorting – The number of waste management plants in Europe that implement visual waste detection systems is steadily growing. Contrarily, Serbian waste management plants are still not exploiting the benefits of this technology.